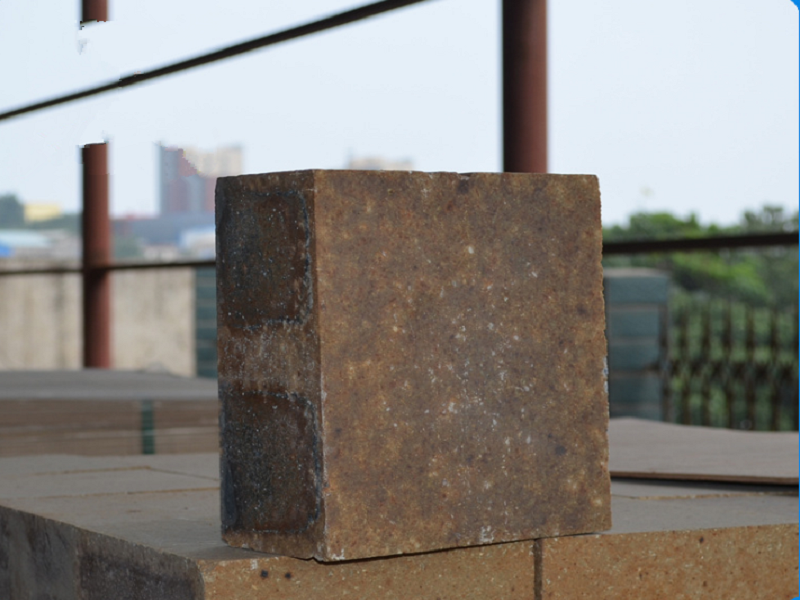
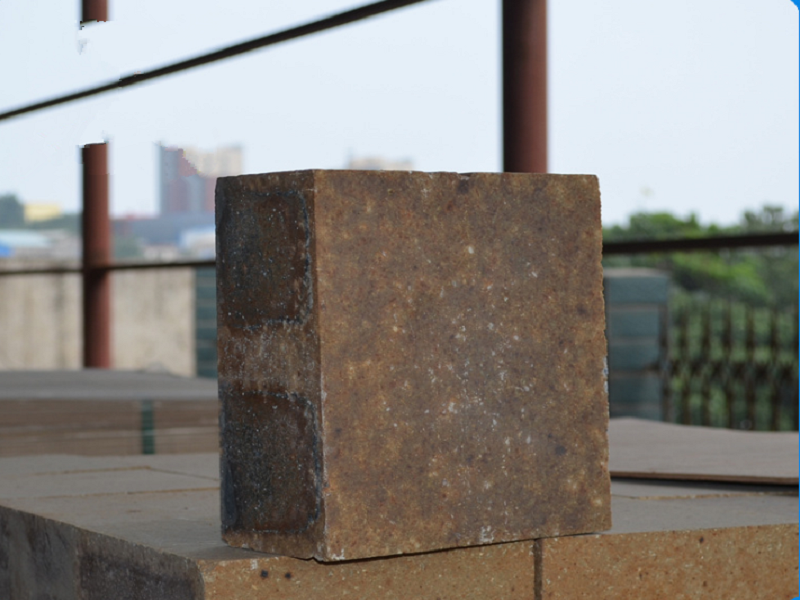
Refractory silica mullite brick
Model Number: hongtai
Certification:
Minimum Order Quantity:
Silica mullite brick production process principle
The process principle of the silica brick used in cement kiln in the production process is as follows:
It is well known that silicon carbide has high refractoriness and is stable at 2600 ° C in a reducing atmosphere; hardness is high (Mohs hardness 9 to 9.5), second only to diamond; thermal conductivity is high [64.4 W (at 500 ° C) m·K) -1, 875 ° C is 41.4 W · (m · K) -1; the coefficient of thermal expansion is relatively small (5.0 × 10 -6 ° C -1). SiC is a covalent bond, there is no so-called sinter, and a new phase is formed by chemical reaction to achieve sintering, that is, reaction sintering. Therefore, silicon carbide products are classified into clay bonding, mullite bonding, and dioxide oxidation according to the bonding phase. Products such as silicon bonding, Si2N2O bonding, Si3N4 bonding, and Sialon bonding. Among them, the strength of mullite and mullite gold fused plastic is high. See Table Si2N2O bonding, Si3N4 bonding, Sialon bonding SiC products and recrystallized silicon carbide products. Although the strength and other indicators are very high, the production technology is complex and the equipment requirements are high. Not only the high cost of the product, but also the high thermal conductivity of the product is not the ideal refractory material for the cement kiln.
In the late 1980s, the study began to study the complex phase refractories of oxides and non-oxides in binary and even ternary systems. As a well-known non-oxide, SiC attracts attention, so corundum bricks, silicon motiles, etc. have been successfully developed. These composite refractories are characterized by higher temperature and high temperature strength than single oxide materials, and oxidation resistance is better than single SiC. The oxidation of these composite materials is protective oxidation, and the SiC of the surface of the material is oxidized to SiO2 on the surface of the material. The formation of a protective layer gradually prevents further penetration of oxygen into the interior of the article. These composite products have a lower firing temperature than a single oxide product and a high product strength.
Production capacity: Our factory actively response to government environmental protection policy, we designed and built the fully automatic controlled high temperature gas tunnel kiln (1700℃), and got capacity of annual output 70,000 tons of high quality refractory products.
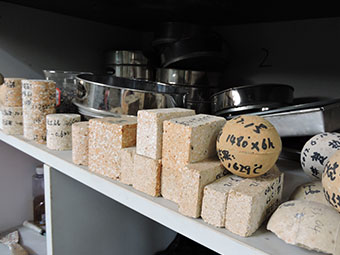
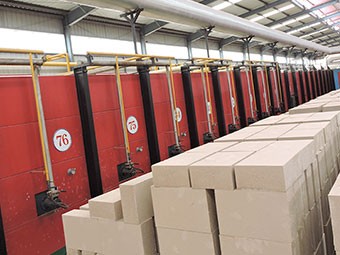
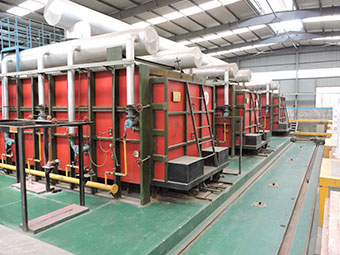
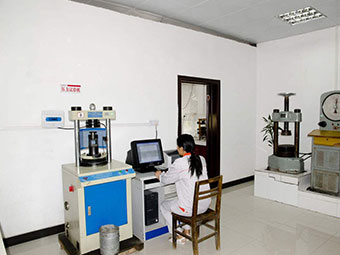
Packing details:
★Bricks: Fumigated wooden pallet with log paperboard covered and stainless steel band strapping, the whole outside is wrapped with thermoplastic film. Or carton packaging.
★Wooden pallet size: usually 92*92cm (standard brick)
★Castable: Ton bag with rain film and 25kg bags inside
★Or according to customer’s requirements
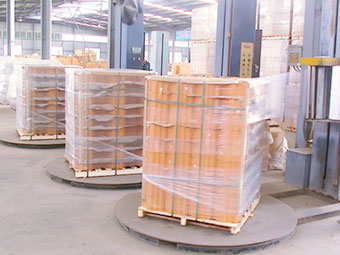
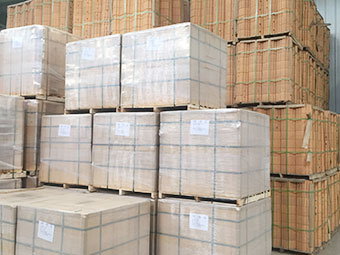
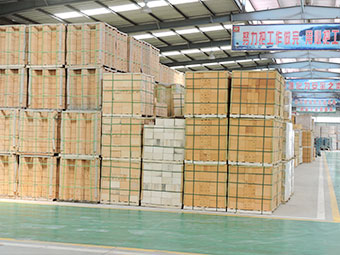
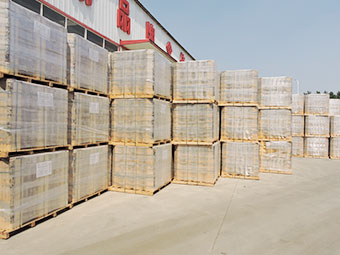
Transportation
★Port of dispatch: Tianjin port; Qingdao port
★Delivery time: According to customer’s demand or two sides negotiate
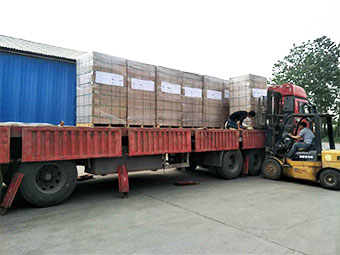
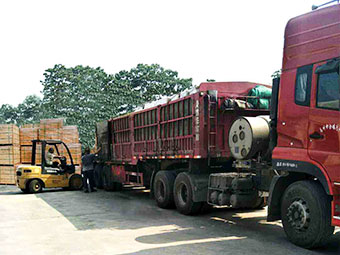
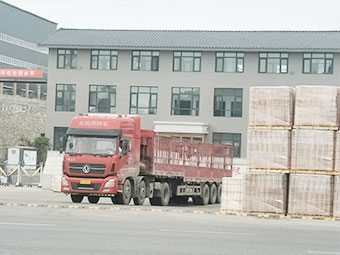
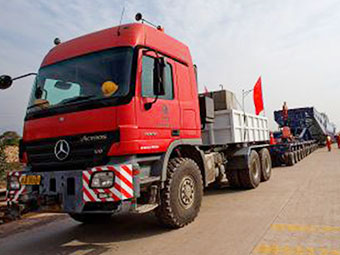
We provide you
★Timely response: Timely response to your inquiry within 24 hours and provide solution.
★Competitive Price: Make the products competitive in your market.
★Free sample: Free sample are offered, trial order are accepted for quality evaluation.
★Strict quality control: We set Quality Management System, from the raw material to finished products, produce high quality products according to chemical & physical specifications strictly to satisfy customers’ needs.
★Fast delivery time: Within 3-30 days according to your quantity after receiving your advance payment.
★ Professional services: Provide pictures from order to delivery. Inspect report by our country’s designated authority and oversea services if necessary.
We are here for you!
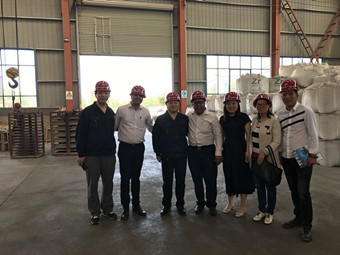
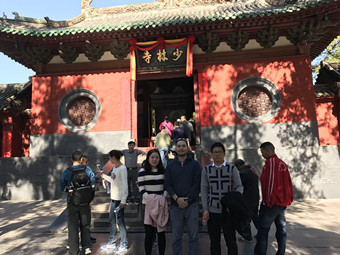
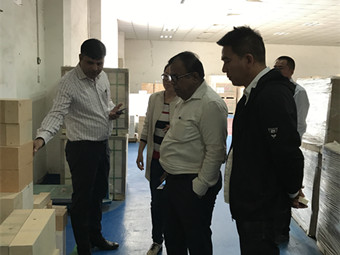
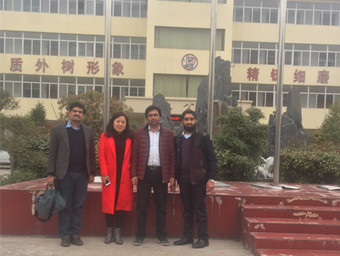
Certification: (ISO 9001:2015)
Please Feel free to give your inquiry in the form below. We will reply you in 24 hours..